Recuperação de Rosca Extrusora: Guia Completo
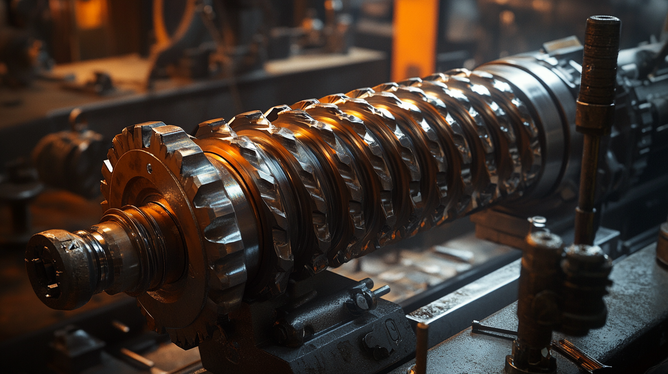
Por: João - 07 de Dezembro de 2024
A recuperação de rosca extrusora é uma prática vital para garantir a eficiência e durabilidade dos sistemas de extrusão. Neste artigo, vamos abordar as principais causas da degradação da rosca, técnicas eficazes para sua recuperação e os benefícios da manutenção preventiva. Continuar lendo é fundamental para entender como prolongar a vida útil do seu equipamento e evitar custos excessivos com substituições.
Causas Comuns da Degradação da Rosca Extrusora
A degradação da rosca extrusora é um fenômeno que pode impactar severamente a produção e a qualidade do produto final na indústria de transformação de plásticos e borrachas. Identificar as causas dessa degradação é o primeiro passo para implementar soluções eficazes e garantir a longevidade do equipamento. Vejamos algumas das causas mais comuns que podem levar à deterioração da rosca extrusora.
1. Desgaste Abrasivo
O desgaste abrasivo ocorre devido ao contato contínuo da rosca com os materiais processados. A abrasividade dos polímeros, especialmente aqueles que contêm aditivos ou cargas, pode lixar as superfícies da rosca, causando Ranhuras e Imperfeições. Com o tempo, esse desgaste pode comprometer a geometria da rosca, resultando em perda de eficiência e aumento da temperatura do processo.
2. Temperatura Elevada
Os processos de extrusão frequentemente operam em temperaturas elevadas. Embora as máquinas sejam projetadas para suportar altas temperaturas, o calor excessivo pode causar deformações térmicas na rosca extrusora. Além disso, temperaturas além do limite adequado para um material específico podem promover reações químicas indesejadas, levando à formação de resíduos que podem obstruir o funcionamento adequado da rosca.
3. Contaminação do Material
A contaminação do material é uma preocupação crucial na extrusão de plásticos. Resíduos de materiais anteriores no cilindro, aditivos não compatíveis ou a presença de umidade podem danificar a rosca. As partículas contaminantes arranham a superfície da rosca e, dependendo da natureza dos contaminantes, podem acelerar o desgaste da rosca e a degradação do material resultante.
4. Falta de Lubrificação
A lubrificação inadequada é uma das principais causas de falhas em equipamentos de extrusão. A falta de lubrificação pode levar ao aumento do atrito entre os componentes, elevando a temperatura de operação e causando desgaste prematuro. É crucial seguir as diretrizes de lubrificação do fabricante e garantir que todas as partes da máquina estejam devidamente lubrificadas para manter seu funcionamento eficiente.
5. Variações na Alimentação do Material
A uniformidade da alimentação do material é essencial para o desempenho da rosca extrusora. Variações significativas na granulometria, umidade ou temperatura do material alimentado podem resultar em grandes pressões dentro do cilindro da extrusora, forçando a rosca a operar além de suas capacidades projetadas. Isso não apenas gera desgaste adicional, mas também pode causar a deformação da rosca ao longo do tempo.
6. Desalinhamento da Máquina
Um desalinhamento entre a rosca e o cilindro pode resultar em um desgaste irregular na rosca extrusora. Isso geralmente ocorre devido a instalação inadequada ou ao desgaste dos suportes e rolamentos que mantêm a rosca em sua posição correta. Um alinhamento incorreto pode causar vibrações excessivas e aumentar o atrito, levando a falhas mais rápidas e à degradação nas superfícies da rosca.
7. Fadiga do Material
A fadiga do material é uma causa comum de degradação que ocorre ao longo do tempo, em resposta à tensão cíclica às quais a rosca é submetida durante seu funcionamento. Esse processo pode levar à formação de microfissuras e, eventualmente, ao colapso estrutural da rosca. Embora o design da rosca leve em consideração a fadiga, condições extremas podem acelerar esse processo.
8. Compatibilidade Química
A incompatibilidade química entre o material processado e a rosca extrusora pode causar degradação significativa. Algumas resinas podem atacar quimicamente os materiais da rosca, levando a corrosão e deterioração. É essencial escolher a rosca adequada para o tipo de material a ser processado, a fim de evitar esse tipo de degradação.
9. Manutenção Inadequada
A falta de manutenção preventiva é um dos principais fatores que contribuem para a degradação da rosca. Rotinas de manutenção inadequadas ou negligenciadas podem resultar em problemas não detectados, que se acumulam ao longo do tempo, levando à falha do equipamento. Estruturas de inspeção regulares e a troca de partes desgastadas em intervalos apropriados são essenciais para manter a rosca extrusora em ótimas condições.
10. Sobrecarga do Equipamento
Utilizar a máquina além de sua capacidade nominal pode causar estresse excessivo na rosca extrusora. Isso pode gerar aquecimento excessivo, deformação e rápido desgaste das superfícies. As especificações do fabricante devem sempre ser seguidas rigorosamente para evitar sobrecarga e danos ao equipamento.
Em resumo, a degradação da rosca extrusora é um problema complexo que pode ser atribuído a diversas causas. Desde o desgaste abrasivo até a manutenção inadequada, entender essas causas é vital para desenvolver estratégias eficazes de recuperação e prolongar a vida útil dos equipamentos. A identificação e a prevenção desses problemas são essenciais para manter a eficiência operacional e evitar custos adicionais decorrentes de falhas e reparos não planejados.
Técnicas Eficazes para Recuperação
A recuperação de roscas extrusoras é essencial para garantir a continuidade da produção e a qualidade do material processado. Com o tempo, as roscas podem sofrer desgastes e danos, mas existem várias técnicas eficazes de recuperação que podem restaurar ou até mesmo melhorar as condições iniciais do equipamento. Neste artigo, vamos explorar as principais técnicas de recuperação que podem ser aplicadas às roscas extrusoras.
1. Rebarbação e Retífica
A rebarbação e a retífica são processos fundamentais para a recuperação de roscas. A rebarbação envolve a remoção de material em excesso e a correção de pequenas imperfeições, enquanto a retífica utiliza máquinas especiais para ajustar a geometria da rosca e das superfícies envolventes. Essas técnicas são eficazes para reparar danos superficiais causados por desgaste abrasivo e garantir que a rosca mantenha a sua eficiência operacional.
2. Recarregamento e Soldagem
Quando o desgaste da rosca é excessivo, o recarregamento pode ser uma solução viável. Nesse processo, um material de soldagem é adicionado às áreas desgastadas, preenchendo fissuras e reestabelecendo a geometria da rosca. Este material deve ser escolhido com cuidado, levando em consideração a compatibilidade com o material original da rosca. Após a soldagem, a área deve ser retificada para garantir um acabamento adequado.
3. Reforço com Placas de Metal
Outra técnica eficaz para a recuperação da rosca extrusora é a aplicação de placas de metal em áreas críticas que estão sujeitas a altos níveis de desgaste. Essas placas são unidas à rosca e oferecem uma camada adicional de proteção contra abrasividade e temperatura. A instalação deve ser feita por profissionais qualificados para garantir que as placas fiquem firmemente unidas e que não afetem a performance da rosca.
4. Tratamentos Térmicos
Os tratamentos térmicos, como têmpera e revenimento, são processos que visam alterar as propriedades mecânicas da rosca. A têmpera aumenta a dureza, enquanto o revenimento pode melhorar a tenacidade e reduzir tensões internas. Estes tratamentos podem ser especialmente benéficos em roscas que já apresentaram desgaste significativo, restaurando características que ajudam a prolongar sua vida útil.
5. Revestimentos ou Reforços Cerâmicos
A aplicação de revestimentos cerâmicos nas roscas extrusoras é uma técnica cada vez mais utilizada para aumentar a resistência ao desgaste. Os revestimentos cerâmicos possuem alta dureza e resistência a materiais abrasivos, tornando-se uma excelente solução para proteger as superfícies da rosca. Esta técnica requer habilidades especiais para a aplicação do revestimento e pode adicionar uma nova camada de proteção que aumenta a durabilidade da rosca.
6. Inspeção e Manutenção Preventiva
Uma abordagem eficaz para a recuperação e manutenção de roscas extrusoras é a implementação de um programa de inspeção e manutenção preventiva. Inspeções regulares permitem que os operadores identifiquem sinais de desgaste ou danos antes que se tornem problemas sérios. Manutenção preventiva, como a lubrificação e alinhamento apropriados, pode reduzir significativamente a degradação e prolongar a vida útil da rosca.
7. Uso de Materiais Já Reciclados
Na recuperação de roscas, o uso de materiais reciclados de alta qualidade pode ser uma opção viável para o recarregamento e reforço de componentes desgastados. Esses materiais normalmente apresentam boas propriedades mecânicas e podem ser uma solução mais econômica. Contudo, é importante verificar a compatibilidade e a qualidade do material reciclado para evitar problemas futuros.
8. Tecnologia de Manutenção Preditiva
A tecnologia de manutenção preditiva utiliza sensores e análise de dados para avaliar as condições da rosca extrusora em tempo real. Esse tipo de tecnologia permite que as equipes de manutenção identifiquem potenciais problemas antes que ocorram, programando intervenções de recuperação conforme necessário. Além disso, as técnicas preditivas ajudam a otimizar os tempos de operação e maximizar a eficiência da máquina.
9. Auxílio de Software de Simulação
A utilização de software de simulação permite que os engenheiros analisem o desempenho da rosca extrusora em diferentes condições operacionais e materiais. Esses programas ajudam a prever como mudanças em design ou operações podem impactar a durabilidade e a eficácia da rosca. Assim, é possível otimizar o projeto e a operação da rosca com base em dados concretos, resultando em menos desgastes.
10. Treinamento de Equipe
Investir em treinamento e capacitação dos operadores e da equipe de manutenção é uma parte crucial para a recuperação eficaz da rosca extrusora. Uma equipe bem treinada é capaz de identificar precocemente problemas e aplicar as técnicas de recuperação necessárias de forma mais eficaz. Além disso, haverá maior consciência sobre boas práticas de operação e manutenção, reduzindo a probabilidade de degradação prematura.
Em resumo, a recuperação de roscas extrusoras é uma prática essencial para manter a eficiência do equipamento e a qualidade dos produtos. As técnicas mencionadas, como rebarbação, soldagem, tratamentos térmicos e revestimentos cerâmicos, oferecem diversas soluções para restaurar e até melhorar as condições operacionais. Além disso, a implementação de um plano de manutenção preditiva, investindo em tecnologia e treinamento, pode contribuir significativamente para a longevidade e eficiência do equipamento. A gestão adequada dessas técnicas proporcionará não apenas redução de custos, mas também melhorias na produtividade e na qualidade de produção.
Benefícios da Manutenção Preventiva
A manutenção preventiva é uma estratégia essencial nas operações industriais, especialmente no que diz respeito à recuperação e preservação de equipamentos, como as roscas extrusoras. Ela não só assegura que o equipamento funcione com eficiência, como também contribui para a sustentabilidade do negócio. Neste artigo, exploraremos os principais benefícios da manutenção preventiva e porque ela deve ser uma prioridade nas indústrias que dependem de roscas extrusoras.
1. Aumento da Vida Útil do Equipamento
Um dos principais benefícios da manutenção preventiva é o aumento da vida útil dos equipamentos. Ao realizar inspeções regulares e pequenos reparos antes que problemas sérios se desenvolvam, os operadores podem evitar desgastes excessivos nas roscas extrusoras. Isso não apenas economiza dinheiro em substituições, mas também garante que os processos de produção não sejam interrompidos por falhas inesperadas.
2. Melhoria da Eficiência Operacional
Um equipamento bem mantido opera de maneira mais eficiente. A manutenção preventiva ajuda a garantir que a rosca extrusora funcione dentro de suas especificações de projeto. Isso melhora não apenas a eficiência do equipamento, mas também a qualidade do produto final. Com uma rosca em perfeito estado, as variáveis de temperatura e pressão são mais estáveis, resultando em menos desvios e uma produção uniforme.
3. Redução de Custos Operacionais
Embora possa parecer que os custos de manutenção preventiva são altos, eles são insignificantes se comparados aos custos resultantes de falhas inesperadas. Os custos de reparos emergenciais, paradas de produção e substituições são geralmente muito mais elevados. Portanto, investir na manutenção preventiva pode resultar em uma economia significativa a longo prazo, permitindo que os recursos financeiros da empresa sejam melhor alocados.
4. Prevenção de Paradas Não Planejadas
As paradas inesperadas podem causar perdas financeiras consideráveis. A manutenção preventiva visa identificar e resolver problemas potenciais antes que eles se tornem falhas catastróficas. Isso minimiza o tempo de inatividade e assegura que as operações sigam conforme o planejado. Com cronogramas de manutenção estabelecidos, as equipes podem programar as paradas durante horários de baixa produção, evitando interrupções que afetam a produtividade.
5. Melhoria na Segurança Operacional
A segurança no ambiente industrial é uma prioridade máxima. Equipamentos mal mantidos podem apresentar riscos, incluindo falhas que podem provocar acidentes. A manutenção preventiva ajuda a identificar e corrigir condições inseguras antes que se tornem um problema. O cuidado com roscas extrusoras e outros componentes reduz não apenas riscos de acidentes, mas também assegura que as normas de segurança estejam sendo cumpridas.
6. Aumento da Satisfação do Cliente
Quando a produção ocorre sem interrupções e a qualidade do produto final é alta, a satisfação do cliente aumenta. A manutenção preventiva contribui para uma operação consistente, resultando em um atendimento melhor e mais confiável. Clientes satisfeitos são mais propensos a retornar e a recomendar a empresa a outros, resultando em um aumento da reputação e dos negócios.
7. Planejamento e Organização Melhorados
A implementação de um programa de manutenção preventiva promove uma cultura de planejamento e organização dentro da empresa. Uma abordagem estruturada para a manutenção impulsiona as equipes a documentar procedimentos, manter registros detalhados e monitorar o desempenho do equipamento. Com essa organização, torna-se mais fácil identificar tendências e desenvolver novas estratégias para melhorar ainda mais a performance.
8. Impacto Ambiental Positivo
A manutenção preventiva também pode criar um impacto positivo no meio ambiente. Equipamentos eficientes consomem menos energia e geram menos resíduos. Ao evitar falhas que poderiam resultar na necessidade de substituições, a manutenção preventiva minimiza o descarte de materiais e componentes e reduz a pegada de carbono da empresa.
9. Facilitação de Treinamentos e Treinamento da Equipe
Manter um cronograma de manutenção preventiva permite que as equipes tenham uma compreensão melhor do funcionamento dos equipamentos. Isso facilita treinamentos mais eficazes e uma formação mais abrangente para novos funcionários. Com uma equipe bien treinada, as operações se tornam mais simples e eficazes, permitindo que todos os colaboradores entendam a importância da manutenção e suas melhores práticas.
10. Identificação de Oportunidades de Melhoria
Durante a manutenção preventiva, os operadores e equipes de manutenção têm a oportunidade de analisar cada parte do equipamento, incluindo a rosca extrusora. Isso permite que identifiquem áreas não apenas que precisam de atenção, mas também oportunidades de melhoria. A implementação de melhorias contínuas no processo de manutenção pode resultar em inovações que aumentam a eficiência e a eficácia do equipamento ao longo do tempo.
Em conclusão, os benefícios da manutenção preventiva são substanciais e abrangem do aumento da vida útil do equipamento à melhoria na qualidade do produto final. A prática garante que as roscas extrusoras e outros equipamentos funcionem de maneira otimizada, elevando a eficiência operacional e reduzindo custos. Para equipes industriais e operadores, investir em medidas de manutenção preventiva não é apenas uma escolha inteligente, mas uma estratégia obrigatória para o sucesso a longo prazo.
Quando Substituir a Rosca Extrusora
A substituição de uma rosca extrusora é uma decisão significativa que pode impactar diretamente a eficiência e a qualidade da produção em operações industriais. Compreender quando é o momento adequado para substituir a rosca é fundamental para evitar paradas não planejadas e desperdícios. Neste artigo, exploraremos as situações e sinais que indicam a necessidade de substituição da rosca extrusora, garantindo que sua operação permaneça otimizada.
1. Desgaste Visível e Medido
Um dos sinais mais claros de que uma rosca extrusora precisa ser substituída é o desgaste visível. A inspeção regular do equipamento deve incluir a busca por rachaduras, deformações e perda de material na superfície da rosca. Além do desgaste visual, medições do diâmetro e do perfil da rosca devem ser feitas. Caso a rosca apresente uma diferença significativa em relação às especificações do fabricante, a substituição se torna iminente.
2. Performance Abaixo do Esperado
Se a extrusora não estiver operando de acordo com os parâmetros ou padrões de produção estabelecidos, pode ser um sinal de que a rosca precisa ser trocada. Uma rosca desgastada pode resultar em uma taxa de extrusão reduzida, variações na espessura do material e dificuldade em manter temperaturas adequadas. Monitorar a performance ao longo do tempo ajudará a identificar quando as quedas de eficiência justificam uma substituição.
3. Aumento da Temperatura de Operação
A temperatura excessiva durante a extrusão pode ser um indicativo de problemas na rosca. Se a máquina estiver apresentando temperaturas mais altas do que o normal, isso pode ser sinal de que a rosca não está funcionando eficientemente, levando a riscos de degradação do material. O calor extra pode causar danos à própria rosca e ainda afetar a qualidade do produto final, tornando a substituição indispensável.
4. Vibrações e Ruídos Incomuns
Vibrações e sons anormais durante a operação são sinais de que algo pode estar errado. Esses problemas podem ser causados por desalinhamentos, desgaste nas roscas ou problemas com os rolamentos. Se as vibrações e ruídos persistirem mesmo após ajustes e manutenção, isso pode indicar um dano mais sério à rosca que justifique a sua substituição.
5. Histórico de Manutenção Constante
Equipamentos que requerem manutenção frequente e intensiva podem ser candidatos à substituição. Se a rosca extrusora tem um histórico de danos repetidos e falhas, é importante avalia-la criticamente. O custo de manutenção contínua pode ultrapassar o custo da nova substituição, e o tempo de inatividade da máquina pode impactar a produtividade da empresa.
6. Alterações no Material Processado
Mudanças nos tipos de materiais que estão sendo utilizados na máquina podem exigir ajustes nas especificações da rosca. Se sua empresa passou a trabalhar com materiais de maior abrasividade ou com características químicas diferentes, isso pode afetar o desempenho da rosca existente. Nestes casos, pode ser necessário substituir a rosca por outra que tenha características que ofereçam maior durabilidade e compatibilidade com os novos materiais.
7. Eficiência Energética Comprometida
Uma rosca extrusora desgastada pode levar a um aumento no consumo de energia, uma vez que a máquina não opera nas suas melhores condições. Se os custos de energia aumentarem sem uma explicação clara, isso pode ser um indicativo de que a rosca precisa ser substituída. Realizar auditorias energéticas para identificar aumentos incomuns nos gastos pode auxiliar na decisão da troca.
8. Quebras e Danos Estruturais
Quebras ou danos estruturais à rosca são eventos extremos que requerem substituição imediata. Isso pode acontecer devido a sobrecargas, falhas de projeto, ou deformações graves. Qualquer dano que comprometa a integridade estrutural da rosca não deve ser ignorado, pois isso pode resultar em falhas na operação e danos adicionais ao equipamento.
9. Compatibilidade com Novas Tecnologias
Com o avanço da tecnologia, pode haver novas roscas no mercado que oferecem melhorias significativas em eficiência, durabilidade e performance. Se a sua rosca atual não estiver acompanhando as inovações do setor, pode ser o momento de considerar uma substituição. Investir em uma rosca mais moderna pode reduzir custos operacionais a longo prazo e aumentar a eficiência da produção.
10. Necessidade de Melhorias na Qualidade do Produto
A qualidade do produto final é um reflexo direto do estado da rosca extrusora. Se houver uma deterioração na qualidade do produto, como irregularidades na espessura ou impurezas, isso pode indicar a necessidade de substituição da rosca. Manter um padrão de qualidade é essencial para satisfazer os clientes e, portanto, qualquer comprometimento dessa qualidade deve ser resolvido rapidamente com a troca do equipamento inadequado.
Em resumo, a decisão de substituir uma rosca extrusora não deve ser tomada de ânimo leve. Existem vários sinais e circunstâncias que podem indicar que a substituição é necessária, incluindo desgaste visível, redução de performance, aumento de temperatura, vibrações anormais, e mudanças nos materiais processados. Uma estratégia bem planejada para monitorar e avaliar o estado da rosca ajudará a garantir operações mais eficientes e a maximizar o retorno sobre o investimento em equipamentos de produção.
A recuperação de rosca extrusora é essencial para a continuidade e a qualidade das operações industriais. Ao compreender as causas da degradação, aplicar técnicas eficazes de recuperação e adotar uma abordagem proativa com a manutenção preventiva, as empresas não apenas melhoram a eficiência de seus sistemas, mas também prolongam a vida útil do equipamento, minimizando custos e interrupções. A troca adequada da rosca, quando necessária, estabelece um ciclo produtivo saudável e sustentável. Investir na recuperação e manutenção adequadas é, sem dúvida, uma estratégia inteligente que resulta em um desempenho superior e na satisfação dos clientes. Portanto, ao manter a atenção em cada um desses aspectos, você garantirá que suas operações de extrusão permaneçam competitivas e altamente eficazes.